Industrial CO2 Emissions and the Path Towards Decarbonization in Indonesia
- Geni Buana Nusantara
- Nov 1, 2024
- 9 min read
Updated: Nov 8, 2024
Various sectors, such as transportation, households, services, agriculture, industry and power generation, contribute to carbon dioxide emissions through energy use. Companies are major contributors to greenhouse gas (GHG) emissions, mainly from fossil fuel combustion and cement production. CO2 emissions, the largest driver of GHGs, have increased significantly in Indonesia since 1990, reaching 581 MtCO2 in 2019. The industrial sector accounted for 37% of total emissions, followed by transportation and power generation at 27% each with data in Figure 1.
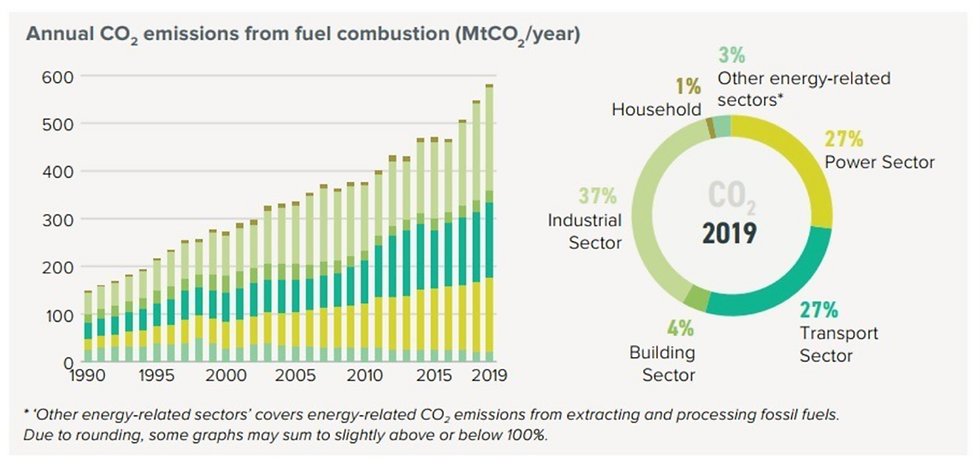
Figure 1. Energy-related CO2 emissions by sector | Source: Climate Accountability Institute Report 2020
In 2014, the World Resources Institute reported that Indonesia ranks as the world's sixth-largest carbon emitter at 1.981 billion tons per year and is the highest carbon emitter in Southeast Asia (Figure 2). This reality has driven Indonesia’s commitment to reducing GHG emissions by ratifying the Kyoto Protocol under Law No. 17 of 2004, targeting reductions in six key greenhouse gases, including CO2.
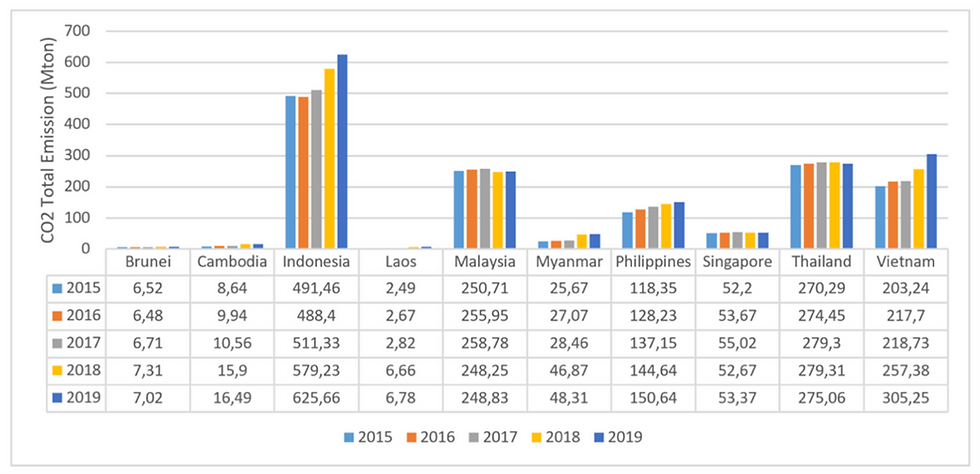
Figure 2. CO2 Emission Trends in Southeast Asia (2015-2019) | Source: Joint Research Centre of the European Union
It has been agreed to phase out fossil fuel subsidies that do not support energy poverty alleviation or a just transition as soon as possible. This agreement will have a significant impact on the parties involved, especially for countries that are still heavily dependent on fossil fuels, such as Indonesia. However, this decision also opens up opportunities for Indonesia to transition away from fossil fuels towards the development of renewable energy sources. This transition process needs to be done with sustainable development and poverty alleviation in mind, so that the benefits of the transition can be felt by all levels of society. Along with these efforts, it is important to realize that CO2 emissions have a significant impact on global warming. One of the main sources of CO2 emissions comes from the industrial sector, especially industries that require large amounts of energy, such as cement, pulp and paper, iron and steel, and the chemical industry. To identify potential CO2 emissions and find opportunities to reduce them, research, field surveys, energy efficiency audits, and recommendations for relevant industries to reduce fuel use are needed. These measures will contribute to the reduction of CO2 gas emissions and reduce the industry's negative impact on the environment. Thus, CO2 emission reduction efforts are in line with the commitment to make a sustainable energy transition. There are several key industrial sectors and their emissions contribution data:
Cement Industry: One of the largest contributors to carbon emissions, the cement manufacturing process generates CO2 emissions due to coal combustion and limestone decomposition. In Indonesia, this sector accounts for about 10-12% of the total national industrial emissions, with Semen Indonesia Group as the main contributor. Globally, cement production accounts for 7-8% of the world's total CO2 emissions.
Steel Industry: Uses coal significantly for smelting iron ore, which results in large CO2 emissions. In Indonesia, the steel sector contributes about 8% of the industry's total emissions, while globally it accounts for 7-9%. PT Krakatau Steel is one of the main producers in this sector.
Pulp and Paper Industry: The pulp and paper manufacturing process is energy-intensive and generates CO2 emissions, mainly from burning fossil fuels. In Indonesia, this sector accounts for around 6-7% of total industry emissions, mainly from companies such as Asia Pulp & Paper (APP) and APRIL Group. Globally, the industry contributes 5-6% of total industry emissions.
Petrochemical and Chemical Sector: Contributes to emissions through fossil fuel combustion and chemical production processes. In Indonesia, this sector is estimated to contribute around 5% of total industrial emissions, while globally it contributes 6-8%. Nitrogen fertilizer production, in particular, generates CO2 and nitrous oxide (N2O) emissions.
Energy and Power Generation: Fossil fuel power generation, particularly coal, is a major contributor to carbon emissions. The energy sector accounts for about 60% of Indonesia's total carbon emissions, with emissions from power plants reaching more than 200 million tons of CO2 in 2020.
Food and Beverage Processing Industry: Despite its lower contribution, this sector still generates emissions from energy use in the production and transportation processes. This sector is estimated to account for around 3-4% of Indonesia's total industrial emissions, as the processed food industry continues to grow.
In the cement industry, about 40% of the total energy consumption is spent on the clinker forming process. Meanwhile, in ammonia manufacturing, cleaning or purification takes up the largest portion of energy, at 50%. In the pulp and paper sector, the drying process absorbs 60% of the total energy used. For the textile industry, 75% of energy consumption comes from heating systems used in textile production. According to the mapping conducted by R & D, the development of decarbonization technologies in Indonesia mostly focuses on basic CCUS technologies, alternative fuels such as biofuels, biomass cofiring, and Refuse Derived Fuel (RDF). On the other hand, power to heat technology has not been widely implemented in Indonesia.
In 2016, the Coordinating Ministry for Economic Affairs estimated that 8 industrial sectors contributed the highest national greenhouse gas (GHG) emissions: pulp and paper, cement, textiles, iron and steel, food and beverages, fertilizers, chemicals, and ceramics and glass, ranked from highest to lowest. These eight sectors combined emitted more than 147 MtCO2e, contributing about 56% of total industrial GHG emissions related to energy use in 2016. Most of the emissions in some of these industries are due to the use of natural gas or coal. For example, in the cement and iron and steel industries, coal is the main cause of emissions, while the ammonia industry is highly dependent on natural gas. In addition, the cement and iron and steel sectors are also important areas to mitigate emissions from non-energy process industries (IPPU).

Figure 3. Industrial GHG emissions in Indonesia (2011-2020) | Source: IESR, 2022.
PT Geni Buana Nusantara has studied “Readiness Assessment in the Adoption of Industry Decarbonization and Advancement in Process Heating Electrification” with IESR. The study found that the 5 industry sectors analyzed have different levels of readiness for decarbonization, depending on their individual characteristics and performance. Although the cement industry has made progress in energy efficiency and the use of alternative fuels, the reduction in greenhouse gas emissions is still limited. In contrast, the pulp and paper sector shows better readiness with the implementation of efficient energy use methods and adherence to strict environmental standards. Some industrial sectors, such as cement, ammonia, iron and steel, pulp and paper, and textiles, are still heavily dependent on fossil fuels. Many companies in these sectors face challenges, such as high costs and regulatory barriers. Electrification can reduce carbon emissions by replacing fossil fuels in production with cleaner electrical energy, especially from renewable sources such as wind, solar and hydro power. This transition could reduce carbon emissions by 30-50% in the industrial sector, depending on the technology used, and support global efforts to achieve net zero emissions.
However, pioneering projects and early adopters, such as that of PT Gunung Raja Paksi in the iron and steel sector, open up opportunities for wider adoption in the future. There are five industry sectors that show significant electrification potential, namely:
Cement industry, with large potential for kiln electrification.
PT Indiocement Tunggal Perkasa, whose electricity demand is 240 MW and heat-to-electricity conversion is about 1,307 MW, while the grid can provide 2,450 MW, so it is still possible to convert electricity to heat. It is found that the energy saving is 31,138.25 TJ/year and the CO2 reduction is about 2,378,740.00 mtCO2/year. For energy savings, the specific energy cost is 0.62 $/ton, making it cheaper without taking capital expenditure into account.
Ammonia industry, which has conventional electrification opportunities through water electrolysis and ammonia synthesis. PT Pupuk Sriwijaya, where the electricity demand is 50 MW and the conversion of heat to electricity is about 3,029 MW, while the grid that provides is only able to provide 343 MW, so there must be an increase in grid voltage or substation to the electricity demand. It was found that the energy saving is 72,646.97 TJ/year and CO2 reduction is about 5,788,357.52 mtCO2/year. For energy savings, the specific energy cost is 6.51 $/ton, making it cheaper without taking capital expenditure into account.
Iron and steel industry, with the potential use of EAF (Electric Arc Furnace) for direct iron reduction process. PT Krakatau Steel, where the electricity demand is 120 MW and the conversion of heat to electricity is about 193 MW, while the grid that provides can provide 735 MW, so it is still very possible to convert electricity to heat. It was found that the energy saving is 4,484.95 TJ/year and the CO2 reduction is about 288,595.60 mtCO2/year. For energy savings, the specific energy cost is 0.05 $/ton, so it is cheaper without taking capital expenditure into account.
Pulp and paper industry, which can utilize low-carbon electricity through steam boiler. PT Indah Kiat Pulp and Paper, where the electricity demand is 60 MW and the conversion of heat to electricity is about 2,787 MW, while the grid that provides is only able to provide 735 MW, so there must be an increase in grid voltage or substation to the electricity demand. It was found that the energy savings amounted to 66,826.83 TJ/year and the CO2 that can be saved is about 5,318,066.56 mtCO2/year. For energy savings, the specific cost is 1.34 $/ton, making it cheaper without taking capital expenditure into account.
Textile industry, which can replace dyeing process with renewable electricity. PT Pan Brother, where the electricity demand is 120 MW and the heat-to-electricity conversion is about 15 MW, while the grid can provide 735 MW, so it is still possible to convert electricity to heat. It was found that the energy saving is 2,898.63 TJ/year and the CO2 reduction is about 203,810.24 mtCO2/year. For energy savings, the specific energy cost is 0.11 $/ton, so it is cheaper without taking capital expenditure into account.
Electrification of this process will impact the power grid in four key aspects, namely peak capacity, integrated resource planning, voltage regulation, and distribution upgrades, which may require upgrading substations to higher voltages in some plants.
Case Study of Decarbonization Pioneers
One of the companies in the largest emitting industry that has already done a lot to decarbonize is Holcim. The company has implemented various innovative technologies, including the use of concrete reinforced with thin prestressed carbon strands, known as Carbon Prestressed Concrete Technology (CPC). The technology not only reduces material usage by 75% compared to conventional methods, but also significantly reduces CO2 emissions. The steps taken by Holcim set an inspiring example for other sectors in the transition to a more sustainable industry. Through the application of technology and best practices, Holcim is committed to reducing its carbon footprint and contributing to global efforts to achieve net zero emissions.
One of the key steps in Holcim's journey towards net zero emissions is the replacement of fossil fuels with alternative fuels, such as biomass and other unused materials. Holcim is systematically innovating to accelerate the use of alternative fuels in cement plants, with some plants in Europe already achieving substitution rates of almost 100%. The use of alternative fuels not only reduces the carbon intensity of cement but also supports a circular economy and reduces dependence on fossil fuels.
Alternative fuels serve to lower the carbon intensity of cement and divert waste from incineration or final disposal.
Cement plants in Europe are leading the way in this regard, with some plants using almost 100% alternative fuels.
Next-generation technologies are also increasing substitution rates.
Clinker, which is the main component of cement, is produced in kilns that require thermal energy. Typically, kilns are heated with fossil fuels, and the combustion of these fuels is responsible for about 40% of CO2 emissions from cement. To reduce carbon intensity, Holcim is replacing fossil fuels with alternatives, including biomass and non-recyclable waste sources. By 2022, alternative fuels account for 28% of Holcim's thermal energy requirements for clinker production. In an effort to increase the substitution of fossil fuels with alternative fuels, Holcim continues to invest in cutting-edge technologies. As part of its zero emission plan, Holcim aims to increase the thermal substitution rate to 50% by 2030 and more than 70% by 2050. By replacing traditional fuels in cement plants with alternative fuels, Holcim can solve several challenges at once, namely:
Reducing dependence on fossil fuels
Lower the carbon intensity of cement products
Provide a safe and environmentally friendly solution for unused waste, by applying the most stringent international waste management standards
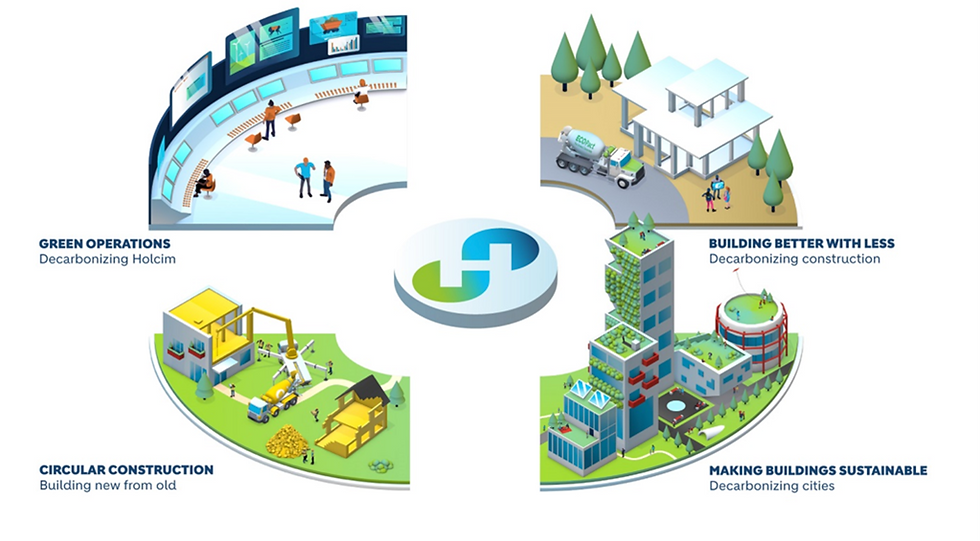
Figure 4. 4 Pillars of Decarbonizing Development.
In a context that increasingly emphasizes sustainability, the industrial sector is faced with significant challenges to reduce carbon emissions. One promising approach is the efficient application of carbon capture technology (CCS). This technology is capable of capturing CO2 emissions generated from various industrial processes before they are released into the air, thereby helping to reduce the carbon footprint. In addition, the integration of renewable energy in the manufacturing process is a crucial step towards reducing dependence on fossil fuels. By utilizing renewable energy sources such as solar and wind power, and implementing advanced distributed energy systems, industries can not only reduce emissions but also improve energy use efficiency. To drive innovation in carbon capture and renewable energy utilization, investment in research and development of new technologies, as well as partnerships with research institutions, is necessary. Regulatory support from the government is also an important factor in creating a favorable climate for the application of these technologies. Through this combination of strategies, the industrial sector can move towards a more sustainable future and contribute to global efforts to deal with climate change.
Commentaires