Learning from Banyumas: Optimizing Waste Management and RDF Production
- Geni Buana Nusantara
- Mar 25
- 8 min read
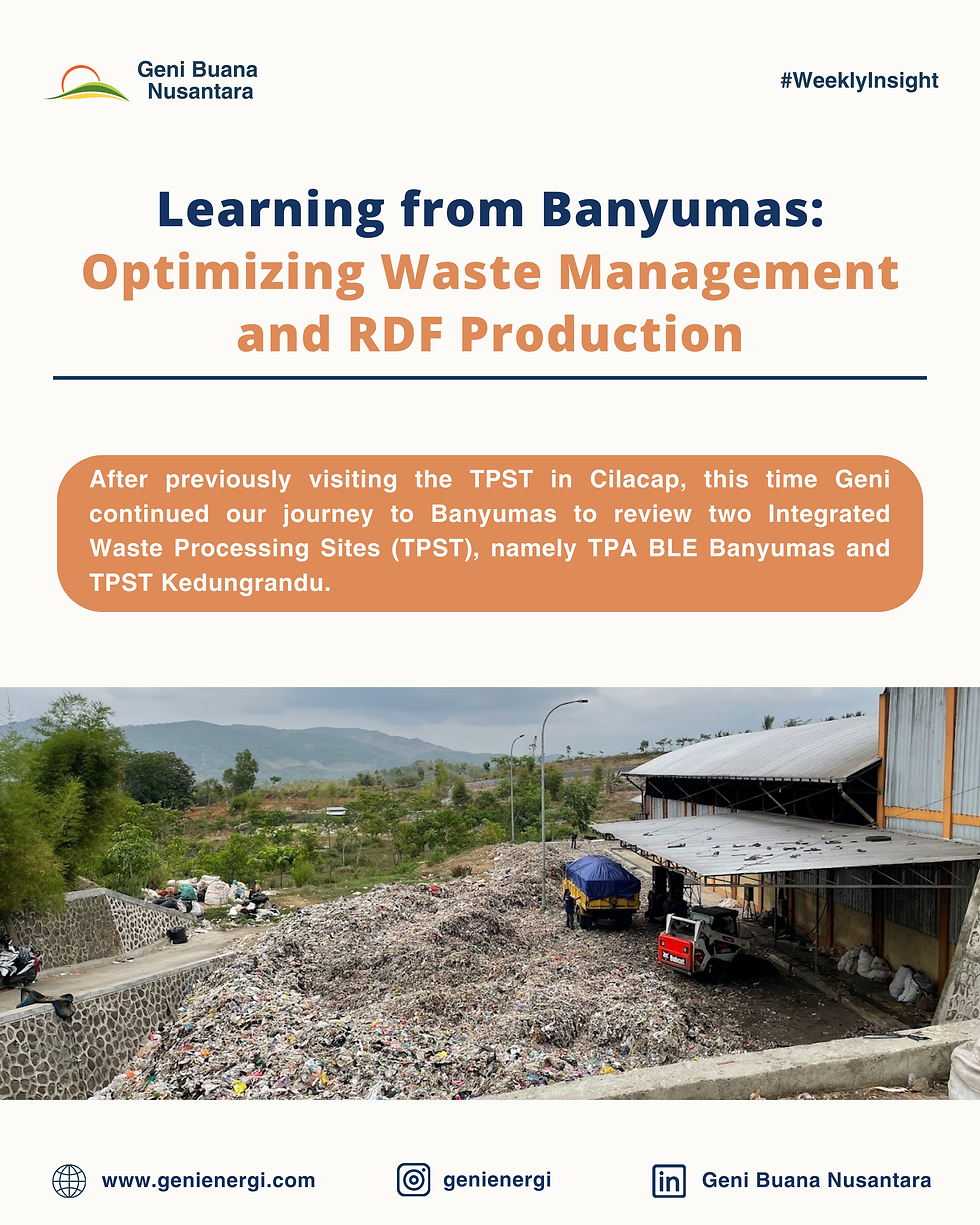
Introduction: Why Banyumas?
After previously visiting the TPST in Cilacap, this time Geni continued our journey to Banyumas to review two Integrated Waste Processing Sites (TPST), namely TPA BLE Banyumas and TPST Kedungrandu. Banyumas Regency has shown a strong commitment to developing a waste to energy processing system. One important initiative is the collaboration between the Banyumas Regency Government, PT PLN Energi Primer Indonesia (PLN EPI), and PT Sinergi Energi Utama to process waste into biomass as raw material for co-firing at the Steam Power Plant (PLTU). This waste processing produces products with economic value such as compost, paving, bricks, plastic pellets, and organic waste pulp used as biomass.
This visit focused on understanding the operational efficiency and challenges faced by the Integrated Waste Processing Site (TPST) in Banyumas Regency, as well as exploring collaboration in the utilization of Refuse Derived Fuel (RDF) with the cement industry such as PT Solusi Bangun Indonesia Tbk (SBI). Several TPSTs in Banyumas, such as TPST Kedungrandu, have demonstrated good management under the auspices of the Banyumas Regency Environmental Service. In addition to managing waste in an integrated manner, TPSTs in Banyumas also process plastic waste into RDF, which can replace coal as fuel in cement factories and contribute to reducing emissions. This effort makes Banyumas an example of a region that is serious about converting waste into a renewable energy source, although challenges such as limited landfill land and less than optimal management still need to be overcome.
To address the problem of plastic waste, the Banyumas Regency Government has collaborated with PT Solusi Bangun Indonesia Tbk (SBI). On August 25, 2021, Banyumas Regent Achmad Husein signed a memorandum of understanding with SBI regarding the use of waste sorting materials as alternative fuels in SBI's cement factory. RDF produced from waste processing at TPST Banyumas is purchased by the SBI cement factory in Cilacap as an alternative fuel. This collaboration not only helps reduce plastic waste in Banyumas but also provides alternative energy sources for the cement industry, thus creating a mutually beneficial relationship between the local government and the industrial sector.
Brief Profile of TPST: BLE Banyumas & Kedung Randu
TPA BLE Banyumas and TPST (Integrated Waste Management Site) Kedungrandu are two waste management facilities in Banyumas Regency that play an important role in managing domestic waste effectively. TPST Kedungrandu serves around 3.100 customers, consisting of 3.067 households and 33 non households, with an average waste management reaching 21.037 tons per day. Meanwhile, TPA BLE Banyumas, also known as TPA BLE Kalibagor, has become a pilot in waste management with the zero waste concept.
In the waste processing process, TPA BLE Banyumas integrates the concepts of circular economy and waste to energy. One of the technologies used is a pyrolysis machine, which is capable of destroying waste through combustion at temperatures above 800oC. Although it is not explicitly stated that TPA BLE Banyumas produces RDF (Refuse Derived Fuel), the use of pyrolysis technology shows an effort to process waste into an alternative energy source. On the other hand, TPST Kedungrandu uses a shredder to process inorganic waste, which is then sold as raw materials for products with economic value.
The existence of these two TPSTs has a positive impact on the environment and the surrounding community. With effective waste management, the volume of waste that ends up in landfills can be reduced, thereby reducing the potential for environmental pollution. In addition, TPST Kedungrandu is able to absorb local workers, with 15 employees. This not only improves environmental quality but also provides economic benefits for the local community.
TPST Kedungrandu: From Waste to RDF
TPST Kedungrandu, managed by the Randu Makmur Community Empowerment Group (KSM), plays an important role in waste management in Banyumas Regency. This facility has a building area of around 1.000 m², with a main area measuring 11,5 × 60 meters and an RDF warehouse measuring 18 × 18 meters. Every day, this TPST processes up to 15 tons of waste from around 3.000 households in Patikraja District and parts of the Purwokerto urban area. The composition of incoming waste consists of 40% organic, 25% plastic (RDF raw material), and 10% residue. The processing process begins with manual sorting, followed by the use of a gibrig machine to separate organic and inorganic waste. Organic waste is processed into compost or maggot feed, while plastic and other inorganic waste are further processed into RDF. The RDF shredder machine at TPST Kedungrandu is currently capable of producing 1 ton of RDF per day, although the potential RDF production reaches 3-4 tons per day. The remaining unprocessed RDF is sent to TPA BLE Banyumas for further processing and then used as alternative fuel in the cement industry such as PT Solusi Bangun Indonesia (SBI).
TPST Kedungrandu has a waste processing system that aims to reduce waste and convert it into alternative fuel. This process begins with sorting incoming waste, then processed according to its type, and finally distributed for further use. The following are the main stages in waste processing at TPST Kedungrandu:
1. Initial Receipt and Sorting
Waste entering the TPST is sorted manually to separate organic and inorganic types.
Inorganic waste is then processed using a gibrig machine to be further destroyed and sorted.
2. Waste Processing Based on Type
Organic waste is processed separately, for example through maggot cultivation or made into compost.
Plastic and inorganic waste are further processed to be converted into Refuse-Derived Fuel (RDF) as an alternative fuel.
3. Distribution and Utilization of RDF
Processed RDF is used as an alternative fuel, such as for PLTU.
If the processing capacity at the TPST Kedungrandu is limited, unprocessed RDF will be sent to another TPST for further processing before use.
TPST Kedungrandu faces several challenges in processing waste into Refuse Derived Fuel (RDF). One of the main obstacles is the limited capacity of the RDF shredder machine, so it cannot process all the available waste potential. As a result, some waste cannot be processed optimally. In addition, the electrical system and equipment at this TPST still often experience technical problems, such as loose fan belts and overheating of the Miniature Circuit Breaker (MCB), which can hamper operations and cause equipment to break down quickly. Limited manpower and infrastructure are also challenges, so some of the RDF produced must be sent to other TPST for further processing. This certainly increases the operational burden and reduces the efficiency of waste management at TPST Kedungrandu.
TPA BLE Banyumas: Larger Scale, Maximum Production & Contract with SBI
TPA BLE Banyumas has a much larger waste processing capacity compared to other TPSTs, with a total capacity reaching 157,5 tons per day. Waste entering this facility is processed into several categories, namely 40 tons of pure waste per day, 45 tons of Refuse-Derived Fuel (RDF) per day, 68 tons of organic pulp per day, and 4,5 tons of residue per day. The RDF produced from this TPST has been contracted and taken by the cement factory PT Solusi Bangun Indonesia (SBI), which uses it as an alternative fuel in the cement production process. In addition, TPA BLE Banyumas also produces biomass that is sold to PT PLN Energi Primer Indonesia (EPI) to be used as a renewable energy source. With a large production scale and optimal utilization of processed waste, TPA BLE Banyumas plays an important role in supporting more sustainable waste management and encouraging a clean energy transition in Indonesia.
The waste processing process at TPA BLE Banyumas is carried out systematically to ensure optimal and environmentally friendly waste utilization. Waste that comes in first goes through a manual sorting stage before being further processed into various products, such as RDF and biomass. Each type of waste has a different processing method, either through shredding, drying, or processing in special facilities. The following are the main stages in the waste processing process at TPA BLE Banyumas.
Initial stage: The incoming waste first goes through a manual sorting process to separate materials that can be further processed. After that, plastic waste and Refuse-Derived Fuel (RDF) materials are shredded so that they are ready to be used as alternative fuels.
Further processing: The remaining waste from 3 dump trucks is further processed in the RDF building to produce alternative fuels for the cement industry, while organic waste is dried in the landfill for one week before being further processed into organic pulp or biomass.
TPA BLE Banyumas continues to innovate in increasing the efficiency of waste processing, but still faces several obstacles. One of the innovations that has been implemented is a SKADA based data logger system to monitor operations automatically. Unfortunately, this system was damaged by rat bites because the installation was carried out underground. To overcome this problem, it is necessary to reinstall it using the above ground method so that it is more durable and not easily damaged. In addition, the main equipment such as the crusher machine, gibrig machine, and RDF shredder require routine maintenance every three days to ensure optimal performance. This maintenance is important to prevent damage that can hinder the waste processing process and RDF production.
A visit to the TPST in Banyumas provided various valuable insights related to waste management that can be applied in other areas. The TPST Banyumas management model shows that with a large capacity and an integrated system, waste processing can be more effective and have a positive impact on the environment. This success can be used as a reference for other areas in developing similar facilities, especially in terms of waste sorting, optimizing RDF production, and utilizing biomass for renewable energy. In addition, the role of the private sector and government is very important in supporting the use of RDF as an alternative fuel. Collaboration between TPST Banyumas and PT Solusi Bangun Indonesia (SBI) in the use of RDF for the cement industry, as well as cooperation with PT PLN Energi Primer Indonesia (EPI) in the use of biomass for co-firing in PLTU, shows that synergy between the government and the business world can accelerate the development of waste to energy solutions. From Geni's perspective, opportunities in the waste to energy and circular economy sectors are increasingly open with regulatory support and increasing awareness of the importance of sustainable waste management. With the right investment and strengthening of supportive policies, this sector has the potential to become one of the main solutions in reducing waste piles while supporting the clean energy transition in Indonesia.
Lessons from Banyumas: What Can Be Applied?
The success of TPST Banyumas in managing waste and producing RDF as an alternative fuel provides many valuable lessons that can be applied in other areas. With a large capacity and cooperation with the private sector, Banyumas has proven that waste processing can not only reduce environmental impacts but also have economic value. However, there are several aspects that can still be improved, both in terms of technology, operational efficiency, and a more sustainable business model. Here are some key points that can be an inspiration for other areas in developing more effective and efficient waste management.
RDF Capacity Expansion
TPST Kedungrandu needs to increase the capacity of the RDF shredding machine so that the processed waste can be used directly without having to be sent to other TPSTs.
Optimization of Machine Maintenance
More frequent maintenance routines at TPST Banyumas can be a reference for increasing operational efficiency and preventing machine damage at other TPSTs.
The Role of Technology in Monitoring
The use of data loggers needs to be improved and implemented in more TPSTs to ensure transparency and increase the efficiency of the waste processing system.
RDF & Biomass Business Opportunities
TPST Banyumas has successfully contracted with SBI for the use of RDF as an alternative fuel in the cement industry. This can be a sustainable business model for other regions that want to develop waste processing into energy.
Challenges in Investment
Although the opportunities are great, investment in RDF and biomass is still relatively high, with profits that may not be maximized. A more mature financial model needs to be developed to make similar projects more attractive to investors.
Conclusion & Future Directions
The sustainability of RDF and biomass-based waste to energy systems requires collaboration from various parties, including the government, private sector, and communities. This synergy is important to ensure that existing technology and infrastructure can be utilized optimally and continue to develop. Geni is committed to continuing to study and develop the best model in supporting low carbon industries in Indonesia, with a focus on innovation and efficiency in waste management. In the future, further exploration will be carried out to see how RDF system integration can be applied on a wider industrial scale and its potential in supporting the renewable energy transition.
Comments