Turning Waste into Energy: How SBI is Leading Indonesia’s Cement Industry Towards a Low Carbon Future
- Geni Buana Nusantara
- Mar 17
- 5 min read
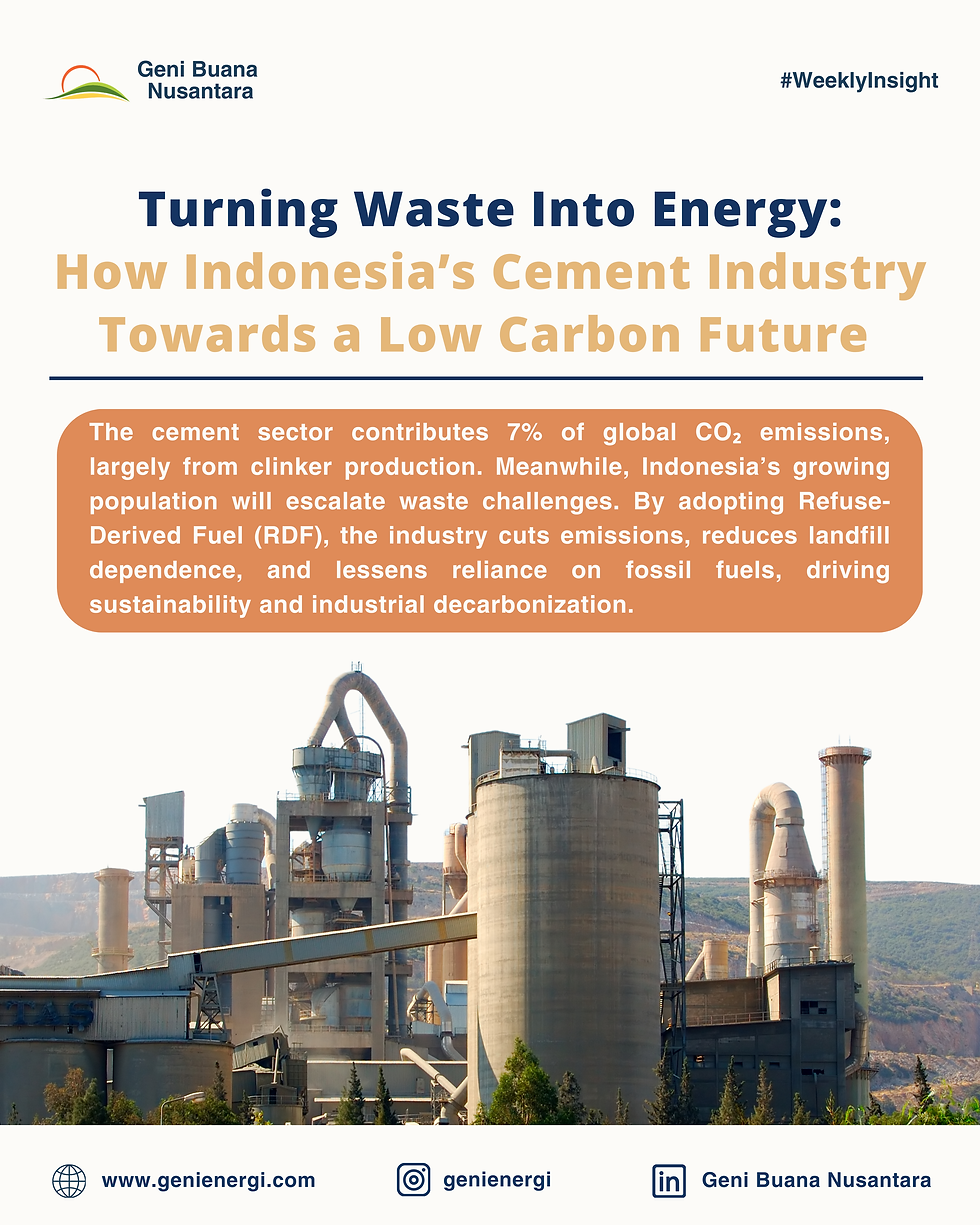
In the second week of February, the Geni team had the opportunity to visit the Integrated Waste Processing Facility (TPST) in Cilacap, join operated with Solusi Bangun Indonesia, to observe firsthand the production process of Refuse Derived Fuel (RDF). From waste piles to alternative fuel, this visit provided valuable insights into waste management innovations in Indonesia. We not only observed the technology in use but also explored the challenges and potential for RDF development in supporting energy transition and industrial decarbonization. The RDF project in Cilacap originated from the initiative of the Cilacap Regency Government, which aimed to address urban waste issues while supporting industrial decarbonization efforts. With an increasing waste volume and limited landfill space, the local government sought more sustainable waste management solutions. Indonesia’s population is projected to reach 319 million by 2045, which will exacerbate waste management challenges, especially in major cities. Currently, landfills (TPA) remain the predominant method for waste disposal, requiring vast land areas and substantial investment. Additionally, landfills pose environmental risks, such as groundwater contamination from leachate and air pollution from unpleasant odors, often facing public resistance.
TPST Cilacap RDF facility offers an innovative waste management solution by converting waste into alternative fuel through shredding and drying processes. The primary objectives of the TPST RDF initiative include reducing landfill dependency, improving environmental quality, and producing an environmentally friendly alternative to coal. The facility, located in Tritih Lor Village, Jeruklegi District, Cilacap Regency, spans three hectares and operates under a multi stakeholder collaboration:
Ministry of Public Works and Housing (PUPR): Provided main building infrastructure. Rp27 billion for infrastructure and supporting facilities.
Ministry of Environment and Forestry (KLHK): Supplied machinery and electrical equipment through a grant from the Danish government. Rp44 billion in mechanical and electrical equipment grants.
Central Java Provincial Government: Provided supporting facilities. Rp10 billion in financial support.
Cilacap Regency Government: Allocated land and access roads. Rp3 billion for land and supporting infrastructure.
SBI acts as the off taker, purchasing RDF for cement production, contributing to both waste management and energy transition efforts. In 2023, SBI utilized 1,66 million tons of waste as alternative fuel, with RDF facility operations expanding to process up to 160 tons per day. SBI and Semen Indonesia Group (SIG) has also established RDF partnerships with the Jakarta Provincial Government, Temanggung, Sleman, and many other Regencies to improve their RDF initiative.
With a waste processing capacity of 120 tons per day, the TPST RDF facility has successfully undergone trials, meeting industry standards. It produces approximately 30-40 tons of RDF daily, reducing moisture content from 57,6% to 22,75% within 21 days, with a calorific value of 3.300 kcal/kg. The RDF processing workflow includes:
Weighing and Reception: Waste is weighed at the weighbridge before being deposited into the receiving area.
Sorting: Waste is segregated into organic and inorganic components.
Pre-treatment: The waste undergoes shredding at a capacity of 40 tons/hour (800 tons/day).
Bio Drying: The shredded material is dried using bio drying technology in nine bays, each with a 500 ton capacity, reducing moisture content to below 25% over a 21 day period.
Screening and Storage: The dried RDF is screened into three fractions: inert materials (<20mm), RDF products (20-50mm), and oversized rejects (>50mm), which are further processed or used as landfill cover.
RDF in Industrial Decarbonization
Cilacap’s RDF facility is a national pilot project in waste to fuel technology. The International Energy Agency (IEA) reports that the cement and concrete sector contributes approximately 7% of global CO₂ emissions, largely from clinker production requiring high temperatures and fossil fuel combustion. PT Solusi Bangun Indonesia (SBI) collaborates with the Cilacap Regency Government in waste management through the TPST RDF facility. Under this partnership, the local government supplies 120 tons of waste daily, which is processed into 40-50 tons of RDF used as an alternative fuel in SBI’s cement kiln. This initiative not only reduces SBI’s reliance on fossil fuels but also lowers CO₂ emissions from cement production. Additionally, it supports sustainable waste management by reducing landfill dependency and optimizing waste as an alternative energy source.
RDF Processing and Environmental Benefits
The RDF production process follows key stages to ensure quality fuel output:
Waste Collection and Supply: Sourced from households, markets, and industries, transported to TPST RDF.
Initial Sorting: Recyclables are separated from organic and inorganic materials.
Shredding and Drying: Waste is shredded and dried to improve calorific value.
Screening and Purification: Contaminants and non-combustible materials are removed.
RDF Formation: Processed waste is converted into fluff, pellets, or briquettes.
Storage and Distribution: RDF is stored before being delivered to cement plants for use as an alternative fuel.
Using RDF offers several environmental advantages, including a 15% reduction in CO₂ emissions, amounting to 582 kg CO₂ per ton of cement equivalent. By diverting waste from landfills and utilizing it as an energy source, RDF contributes to both waste management efficiency and energy sustainability. The national target is to use 1,5 million tons of waste annually as alternative fuel, further enhancing resource efficiency. However, additional data is needed to quantify the specific emission reductions from RDF utilization.
Challenges and Opportunities in RDF Development
Despite its benefits, RDF implementation faces challenges, including regulatory uncertainties, inconsistent waste supply quality, and long term project sustainability. The absence of clear RDF quality standards and limited incentives for industries adopting alternative fuels hinder wider adoption. Additionally, maintaining a stable waste supply with the right composition remains a challenge due to inefficiencies in local waste management systems.
To address these challenges, efforts are underway to enhance RDF production capacity, optimize processing technology, and expand RDF facilities across different regions. Expansion opportunities exist in areas with high waste volumes and significant industrial energy demands. Successful implementation requires strong partnerships between the private sector and government, as well as community engagement in effective waste management practices.
Expanding RDF Utilization in Indonesia
Several regions beyond Cilacap are adopting RDF technology. Jakarta, for instance, operates an RDF facility at the Bantargebang Integrated Waste Processing Site (TPST). This facility processes 1.000 tons of old waste and 1.000 tons of new waste daily, producing approximately 700-750 tons of RDF per day. The RDF facility in Bantargebang follows similar processing steps, including waste sorting, shredding, drying, and fuel conversion, with output used in cement kilns as an alternative to coal.
The Bantargebang RDF initiative is a collaboration between Jakarta’s Environmental Agency, PT Solusi Bangun Indonesia, and PT Indocement Tunggal Prakarsa Tbk, demonstrating a successful public private partnership model. By reducing landfill waste and providing sustainable energy sources for industry, RDF is emerging as a crucial element in Indonesia’s circular economy and energy transition strategy. Future expansion and government incentives will be key to accelerating RDF adoption nationwide, ensuring long term sustainability and environmental benefits.
Comments